粉体の異物検査の方法や異物混入対策などについて
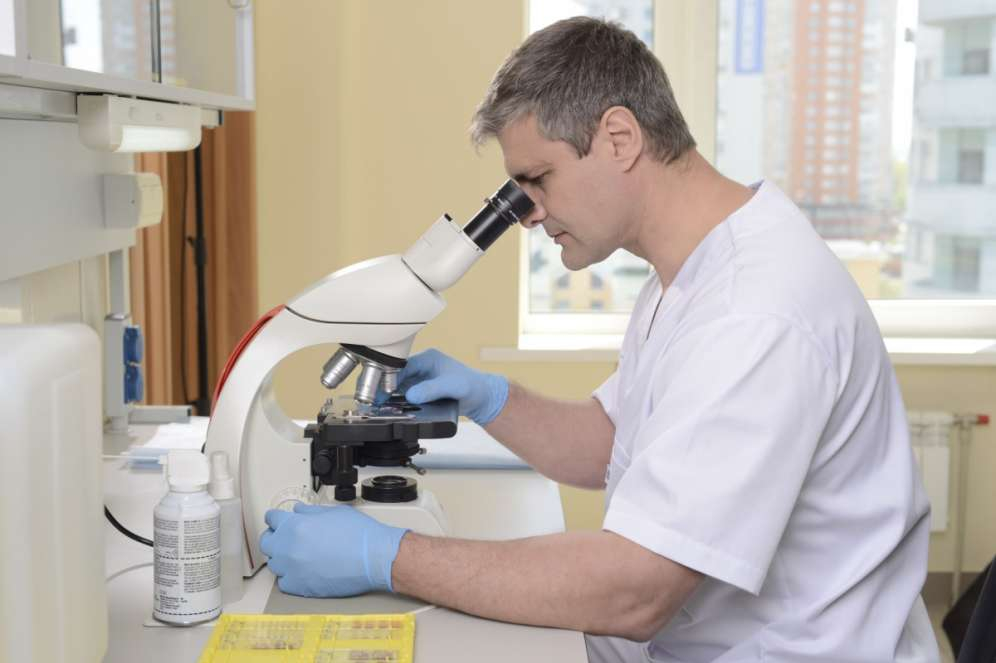
粉体を扱う企業は多く、例えば小麦粉など食品に分類される物やビル建築などで使用するセメントなども粉体です。参照元...食品異物検査
これら粉体は均質状態で原料や製品として供給されますが、該当成分以外は製造過程で除外する必要があります。特に食品は口から人体に入るので、製造工程の内外で混入する異物は大問題で、最悪は製造停止や訴訟問題に発展しかねません。
そこで異物が混入しないように、その対策と検査が行われ粉体の品質が保証されます。
粉体に混入する可能性のある異物とは
粉体にはいろいろありますが、分かりやすくするために以降は食品の粉体で説明していきます。食品の粉体に混入するものとして、物理的なものでは製造工程の劣化や摩耗による、設備の金属片混入などが考えられます。また食品を取り扱うので、製造工程外部から害虫などの侵入も想定できます。
また受け入れ原料自体に、最初から異物が入っている可能性も捨てきれません。更に異物そのものはない、或いは異物があって除去できたとしても正常な状態の原料粉体から室内環境によっては微生物の影響でカビなどが発生し、製造工程内部で異物を作り出してしまうという恐れもあります。
このように物理的または生物的な要因だけでなく、化学的あるいは人間が持ち込んだものなどが異物として混入する、人間的要因さえ存在するので注意が必要です。
金属片なら金属検出装置が使える
粉体の食品製造工程では、基本的に金属でできた自動機械や、搬送用のガイドラインなどに金属を用いています。それが初期不良や長い間使用している間に劣化や摩耗を起こし、金属片として混入してしまうことがあります。
設備で使用しているボルトネジやナットも金属であり、食品の粉体にとっては異物に該当します。金属片にもアルミと鉄や銅でできたものもあり、材質もさまざまです。また製造工程における粉体輸送の装置では、パイプを使用して粉を吸引しながら輸送したり、ベルトコンベアで搬送する場合もあって、金属検出器を取り付けるにしても厳しい条件であったり、流れる粉体のスピードに合わせた適切な検出器の選定が必要になります。
金属検出器の原理は、基本的には検出器の中にあるコイルから金属片に対して過電流を発生させて、金属片の近傍に磁界を発生させます。この磁界の変化を検出器が捉えて、金属片の存在を判定することが可能になります。電気を通さない食品粉体の場合は磁界が発生しないので、何も変化は起こりません。
粉体にどんなに小さな金属が含まれていても、磁界の変化が発生するので、それを異物として認識して検出することができるのです。
異物は金属片だけではなくその除去も必要
そもそも異物は金属片だけとは限りません。異物の種類には、金属でないビニール片とプラスチック片や害虫などの生物の場合があります。これらは磁気を用いた検出法では対処が困難です。そこで登場するのが、蛍光X線を用いた検出器です。
これはX線ビームを粉体に照射したとき、混入している異物にX線が当たるとX線の一部が物質を透過して透過X線となり、一部は反射して蛍光X線になります。異物に含まれる元素は固有のエネルギーを持っているので、反射した蛍光X線からそのエネルギーを検出して異物の元素を割り出し、物質の組成も分かるという優れものです。
また同時に透過X線を利用して分析も行えるので、より詳細な物質特定が可能になり、どの設備に附属していた金属なのかというように異物混入の原因追及にも役立てることができます。もし当該異物の物質が製造工程内になければ、外部からの混入の疑いが濃厚になるという具合です。
製造工程では原料が流れている間に異物除去も必要
食品の粉体原料に初めから混入している異物を含めて、金属片を検出するだけでは異物混入と除去の問題は解決しません。また金属以外の異物の検出を可能にしても、異物発見の精度向上に繋がるものの食品製造工程は異物発見の度に停止せざるを得なくなります。
これでは製造効率が悪くなり製品の原価率も上がって、利益や市場競争力も低下してしまいます。如何に異物を発見して製造工程を止めずに済ますか、言い換えれば異物発見と異物除去を同時に行う工夫を施し、できるだけ連続的に製造することが大事になります。
そこで粉体が流れている間に、どんな異物も検出しながら除去してしまうことが必要です。その除去方法として風の力を利用するというものがあります。
これは私達の日常生活の中でも見ることができます。
それは掃除機の原理です。掃除機には紙パック式やサイクロン方式がありますが、紙パック式はそれがフィルターとなり、ごみと一緒に吸い込んだ空気だけフィルターから通して、通過しなかった細かいゴミをフィルターの中に残して気体と物質を分離します。
またサイクロン方式もゴミと一緒に空気を吸い込み、サイクロンの中で空気が流れている間に遠心力を利用しながら粉体より大きな異物だけを分離し、空気と粉体が抜けて異物の除去が可能になります。このサイクロン方式も気体と物質の分離です。
食品の粉体では、これらフィルター方式とサイクロン方式を組合わせて、まず粉体よりも大きなメッシュのフィルターで粗い異物を除去し、粉体に近い大きさの異物や更に細かい異物をサイクロンでふるい落としながら、目的の粉体だけ分離していき均質な粉体を作り出します。
製造工程の異物に対する更に必要な考え方とは
食品の粉体に限らず異物を検出してそれを除去するだけでは、より高パフォーマンスな製造は実現できません。そのためには異物の検出と除去に加えて、異物になるものを入れないことや持ち込まないということが必要になってきます。
異物検出の精度を高めて除去を確実にしても、本来異物でないものが製造現場にあれば、それが異物になる可能性は排除できません。そこで異物の可能性さえも入れない持ち込まないという考え方が重要になります。食品製造工程では衛生管理上、設備の洗浄は必須です。
そのため腐食しにくい金属が用いられるので、それが劣化したり摩耗して異物発生の原因を作り出してしまうことは避けられません。異物になるものを入れない持ち込まないという考えに則れば、金属を使用している設備はその考え方に逆行してしまいます。
しかしその設備をやめるわけにはいきません。そこで対策として出て来るのが、基本的なことですが定期的なメンテナンスです。メンテナンスは修繕を意味し、故障したときに修理するのもメンテナンスの一つです。このメンテナンスを、故障やトラブルが起こる前に行うのが定期的メンテナンスです。
十分整備された設備はトラブル頻度も少なく抑えることができ、日常点検で異常個所を早期発見することで、更に設備の停止も防げて生産効率が上がります。ひいては設備の破損などによる金属片の粉体への混入も防ぐことに繋がっていきます。
粉体の異物混入問題はトータルで対処する
粉体の製造工程では、異物の検出やその除去を設備で自動的に行います。それだけでなく異物混入の可能性を可能な限り排除するために、人が行う設備保全といった工程管理と統合し、異物混入問題に初めて対処できるということを頭に入れておくこともとても重要です。